The Best of Flow Reps. Straight to your inbox.
A Monthly Email Packed With SOLUTIONS! Not decision.
Thank you! Your submission has been received!
Oops! Something went wrong while submitting the form.
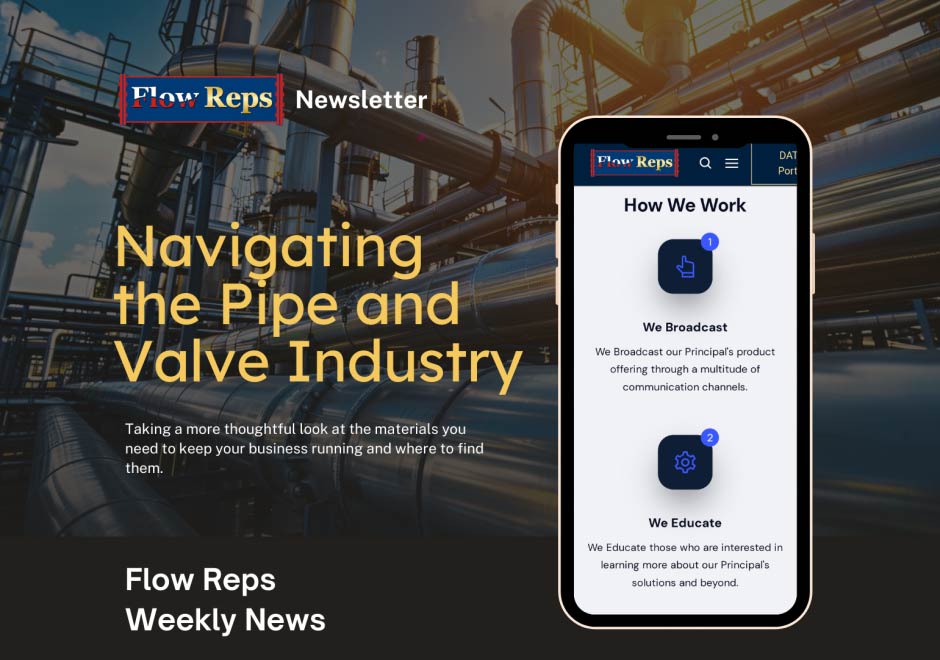
Q&A Resource
Answer
KEY TAKEAWAYS
A rotary actuator is a device that generates rotational motion to turn a shaft or mechanism, commonly used for quarter-turn valves like ball or butterfly valves. Think of a rotary actuator like a doorknob—when you turn it, it rotates around a central axis to open or close the door, just as a rotary actuator turns a valve stem or mechanism. A linear actuator is a device that produces straight-line motion to move a load along a single axis, often used for gate or globe valves requiring linear stem movement. A linear actuator is like a sliding drawer—when you pull or push it, the motion is straight and linear, just like moving a valve stem in or out to control flow.
Rotary and linear actuation are two fundamental types of mechanical motion control used in various industrial applications, including valve automation, robotics, and manufacturing systems. Here’s a breakdown of their differences, characteristics, and uses:
Understanding the specific requirements of the application—such as load, speed, precision, and available space—will help determine which type of actuation is most appropriate.